Highly resistant architectural coating styrene acrylic emulsion BC-992
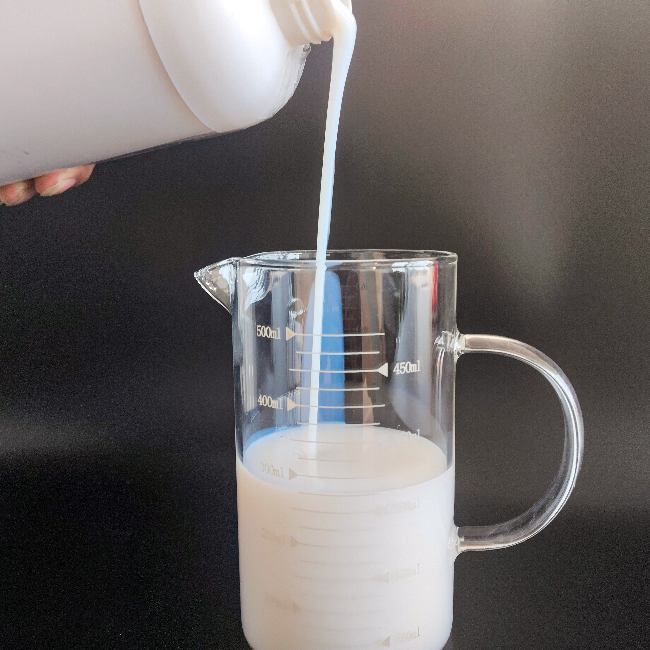
High-durability architectural coatings: Protecting the architectural style and resisting the erosion of time
1. Product Overview
High-durability building coatings refer to a class of advanced coating materials specifically designed to withstand the harshest environmental conditions while maintaining excellent aesthetic and protective properties over an extended period. These coatings are typically formulated with a complex blend of high-quality resins, pigments, fillers, and additives. They come in various forms, such as water-based emulsions, solvent-borne systems, and powder coatings, each tailored to meet different application requirements. Although not represented by a single CAS number due to their multi-component nature, they are meticulously engineered to offer superior performance compared to conventional building coatings.
2. Functional Characteristics
(1) Exceptional Weather Resistance
These coatings possess outstanding resistance to ultraviolet (UV) radiation, which is a major culprit in coating degradation. In a long-term exposure test conducted by an independent research institute in Arizona, known for its intense sunlight and extreme climate, high-durability coatings demonstrated a minimal color change of less than ΔE 3 after 10 years of continuous outdoor exposure, while ordinary acrylic coatings showed a color shift of over ΔE 10 within the same period. The advanced UV absorbers and stabilizers incorporated in their formulation effectively prevent photo-oxidation and chalking, ensuring the coating retains its original appearance and integrity.
(2) Superior Corrosion Resistance
Ideal for protecting metal substrates in coastal and industrial areas, high-durability coatings form a dense, impermeable barrier against moisture, salt spray, and chemical pollutants. For example, in a steel structure located near a chemical plant in Houston, Texas, where the air is laden with corrosive gases and high humidity prevails, a high-durability epoxy-based coating was applied. After 15 years of service, the steel showed no signs of rust or corrosion, maintaining its structural strength, whereas uncoated steel in the vicinity had severe rust damage and required costly repairs or replacement.
(3) Excellent Adhesion
They exhibit remarkable adhesion to a wide range of building substrates, including concrete, masonry, wood, and metal. The polar functional groups in the coating resins interact strongly with the surface of substrates, ensuring a firm bond. In a pull-off adhesion test on concrete surfaces, high-durability coatings achieved an average adhesion strength of over 2.5 MPa, which is significantly higher than the 1.5 MPa of standard coatings, reducing the risk of delamination and flaking even under extreme mechanical stress or temperature fluctuations.
(4) Hydrophobic and Self-Cleaning Properties
Many high-durability coatings feature a hydrophobic surface with a water contact angle greater than 110 degrees. Rainwater rolls off the coated surface, taking away dirt and pollutants, keeping the building facade clean and maintaining its visual appeal. In urban areas with heavy air pollution, buildings coated with self-cleaning high-durability coatings require less frequent cleaning, saving both time and resources. For instance, a commercial building in Beijing, China, with such coatings on its exterior, maintained a clean appearance throughout the year with only occasional light washing during the rainy season, compared to neighboring buildings without self-cleaning coatings that needed regular manual cleaning every few months.
3. Application Fields
(1) Architectural Exteriors
From skyscrapers in bustling metropolises to residential villas in suburban areas, high-durability coatings are widely used to beautify and protect building facades. In Dubai, the iconic Burj Khalifa, the tallest building in the world, is coated with a high-performance fluorocarbon-based high-durability coating. This coating not only withstands the scorching desert sun, sandstorms, and high humidity but also gives the building its gleaming, silver-white appearance that has remained intact for over a decade, enhancing the city's skyline and setting a benchmark for architectural aesthetics and durability.
(2) Industrial Structures
In factories, power plants, bridges, and other industrial facilities, where structures are constantly exposed to chemical fumes, heavy machinery vibrations, and extreme weather conditions, high-durability coatings play a crucial role in corrosion prevention and asset protection. The Golden Gate Bridge in San Francisco, USA, is regularly maintained with high-durability coatings to combat the corrosive effects of the salty sea air and heavy traffic-induced vibrations. The coatings ensure the bridge's structural integrity, prolong its service life, and reduce the need for costly and time-consuming repairs, safeguarding the daily commute of thousands of people.
(3) Coastal Constructions
Coastal regions with their salty sea spray, high winds, and humid climates pose a significant challenge to building materials. High-durability coatings are the go-to solution for seaside resorts, lighthouses, and coastal residential buildings. In the Mediterranean coast, many luxury beachfront villas are protected by silicone-modified high-durability coatings. These coatings resist salt penetration, prevent the growth of mold and mildew due to humidity, and keep the buildings looking fresh and new, even after years of exposure to the harsh coastal environment.
4. Usage Methods
(1) Surface Preparation
Before application, the substrate surface must be thoroughly cleaned, removing dirt, grease, loose paint, and other contaminants. For metal surfaces, sandblasting or chemical etching may be required to create a rough profile for better adhesion. Concrete surfaces should be cured properly and any cracks or holes repaired with suitable fillers. In the case of a new steel bridge construction, the steel components are first shot blasted to a Sa 2.5 surface roughness standard, ensuring a clean and receptive surface for the coating.
(2) Coating Application
High-durability coatings can be applied using various methods depending on the project scale and substrate type. Spray application is commonly used for large areas such as building facades and industrial structures, with airless spray guns adjusted to the appropriate pressure (usually 100 - 300 psi) and spray pattern to achieve an even coating thickness. Roller coating and brush coating are suitable for smaller, more detailed areas or for touch-ups. For example, in a residential painting project, rollers are often used for the main walls, while brushes are employed for edges and corners. Multiple coats are typically applied, with each coat allowed to dry thoroughly according to the manufacturer's recommended drying time, usually ranging from 2 to 24 hours depending on the coating type and environmental conditions. The total dry film thickness is carefully controlled to ensure optimal protection, typically ranging from 0.1 to 0.5 mm for different applications.
(3) Curing and Drying
Proper curing is essential for the coating to develop its full performance potential. Water-based coatings rely on air drying and sometimes additional heat curing at temperatures between 40 - 80°C to accelerate the process and improve film hardness. Solvent-borne coatings dry through solvent evaporation followed by a chemical cross-linking reaction, which may require ventilation to ensure the safe removal of solvents. Powder coatings are cured by heating the coated substrate to temperatures around 180 - 220°C in an oven for a specific period, usually 10 - 30 minutes, to melt and fuse the powder particles into a continuous, durable film.
5. Advantages and Highlights
(1) Long Service Life
High-durability coatings can offer a service life of up to 20 years or more under normal outdoor conditions, significantly reducing the frequency of recoating compared to traditional coatings that may need replacement every 5 - 10 years. This not only saves on coating materials and labor costs but also minimizes disruption to building occupants and operations. For a commercial office building in London, the initial investment in high-durability coatings paid off over the long term as it avoided the need for costly facade repainting for nearly two decades, while adjacent buildings with standard coatings had to undergo multiple recoating projects during the same period.
(2) Environmental Friendliness
Many modern high-durability coatings are water-based or have low volatile organic compound (VOC) content, complying with strict environmental regulations. They emit fewer harmful gases during application and curing, reducing air pollution and improving indoor air quality for construction workers and building occupants. In the European Union, where strict VOC limits are enforced, high-durability water-based coatings have gained popularity due to their ability to meet the stringent environmental standards while providing excellent performance, contributing to sustainable construction practices.
(3) Aesthetic Versatility
Available in a wide range of colors, finishes (such as matte, satin, and gloss), and textures, high-durability coatings can satisfy diverse architectural and design requirements. Architects can choose from an extensive color palette to create unique visual effects on building facades, while the ability to mimic natural materials like stone or wood textures adds an extra dimension to building design. In Singapore's urban landscape, many modern condominiums use high-durability coatings with custom textures to achieve a luxurious and distinctive look that stands out in the city's competitive real estate market.
(4) Cost-Effectiveness in the Long Run
Despite a relatively higher initial cost compared to conventional coatings, the extended service life and reduced maintenance requirements make high-durability coatings a cost-effective choice in the long term. A cost analysis study by a construction consultancy firm showed that over a 20-year period, the total cost of using high-durability coatings, including initial purchase, application, and minimal maintenance, was approximately 30% lower than that of using traditional coatings with their more frequent recoating and associated labor costs.
6. Our Export Advantages
(1) Technological Leadership
Our company has invested heavily in research and development, collaborating with leading research institutions and industry experts. We have developed proprietary formulations that incorporate the latest advancements in polymer chemistry and nanotechnology, resulting in coatings with enhanced performance characteristics. Our patented anti-corrosion additives and UV-resistant nanoparticles have been proven to outperform competitors' products in independent laboratory tests, giving our coatings an edge in the global market.
(2) Quality Assurance
We operate a state-of-the-art manufacturing facility equipped with advanced quality control systems. From raw material sourcing to the final product packaging, every step is rigorously monitored to ensure consistent quality. Our coatings comply with international standards such as ISO 12944 for corrosion protection and ASTM standards for coating performance. We have obtained certifications from major international accreditation bodies, which has facilitated our entry into over 80 countries worldwide, building trust with customers across continents.
(3) Customization Capability
Understanding the diverse needs of different regions and projects, we offer a high level of customization. Whether it's adapting the coating formulation to meet the extreme cold conditions in the Arctic regions, the high humidity of tropical rainforests, or the specific color preferences of local cultures, our R&D team works closely with clients to develop tailor-made solutions. For a construction project in the Sahara Desert, we customized a coating with enhanced sand and heat resistance, ensuring its durability and performance in that unique environment.
(4) Efficient Supply Chain
Located in a strategic industrial zone with excellent transportation links, our production base enables us to ensure prompt delivery of orders. We have established partnerships with global logistics providers to guarantee timely shipping to any destination. Our inventory management system allows us to maintain optimal stock levels, meeting both small and large order requirements with short lead times, which is especially crucial for overseas projects with tight schedules.
7. Summary
High-durability building coatings represent a significant leap forward in the field of construction materials. Their exceptional functional properties, wide application range, and numerous advantages have transformed the way buildings are protected and beautified. With our company's technological prowess, quality assurance, customization capabilities, and efficient supply chain, we are well-positioned to meet the growing global demand for these coatings. As the construction industry continues to evolve towards sustainability and durability, high-durability building coatings will undoubtedly play an increasingly prominent role, enhancing the longevity and visual appeal of structures around the world. By choosing these coatings, builders, architects, and property owners can make a sound investment that pays off in the long term, both aesthetically and economically, while also contributing to a more sustainable built environment.